Densification and Enhancement of Thermomechanical Properties of 3D SiC Using Silica Nanowire Growth Modeling & In-Situ Mineralization Technique
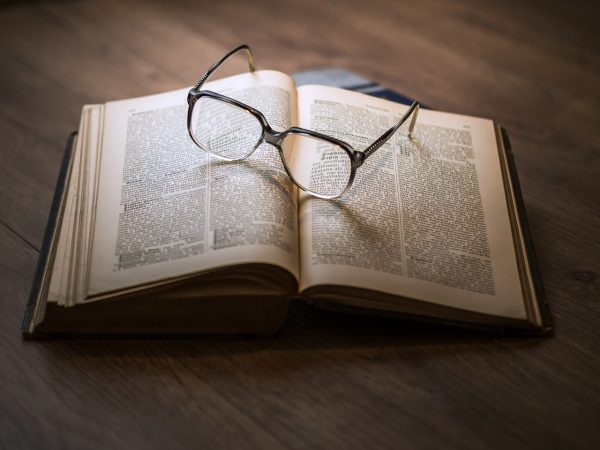
Doctoral Candidate Name: Farjana Sultana
Program: Mechanical Engineering
Defense Date and Time: February 26, 2024 – 10:00 AM
Defense Location: Duke 324
Committee chair’s Name: Dr. Ahmed El-Ghannam
Committee Members: Dr. Harish Cherukuri, Dr. Qiuming Wei, Dr. Youxing Chen, Dr. Ian Marriott
Abstract:
Silicon carbide (SiC) has excellent thermomechanical properties, and it is one of the most promising candidates for many demanding high temperature applications in military, aerospace, space mirrors, nuclear energy stations, filtering, and furnace. Manufacturing of SiC product is difficult due to its thermochemical and mechanical stabilities. The additive manufacturing (AM) of SiC has drawn a lot of attention in recent years due to these excellent materials properties and diverse applications. Previous studies from our lab have shown that the creation of a silica gel layer on the surface of SiC using NaOH solution activated the surface and allowed 3D printing of SiC using water based binder in a powder bed binder jet printer. The dried silica gel layer binds adjacent SiC particles upon hydration during 3D printing at room temperature. The 3D printed green parts require a secondary surface activation by impregnating in NaOH solution and thermal treatment to enhance density and strength. The secondary surface activation technique creates an additional silica layer on the surface of SiC at room temperature which can lead to the growth of silica nanowire inside the pore of 3D printed SiC parts upon heat treatment. The hypotheses underlying this approach are twofold: (i) maximum growth of the silica nanowires will facilitate densification and mechanical properties, and (ii) The silica gel layer can mediate a strong bond between SiC and silicate minerals such as mullite. This thesis has three main objectives. First to understand the effect of processing parameters including concentration of NaOH, thermal treatment temperature and dwelling time on silica nanowires growth and subsequent density and mechanical properties, second, to develop and validate a mathematical model for silica nanowires’ growth and ceramic strengthening, and the third objective is to examine the role of the silica gel layer and thermal treatment parameters on in situ mineralization of mullite bonding agent for SiC composite. This thesis is structured into two parts: (i) experimentally optimizing the processing parameters for silica (SiO2) nanowire growth inside the pore of 3D printed SiC discs based on quantitative SEM analysis and development of a mathematical growth model for silica nanowire growth, and (ii) creating in situ synthesized liquid mullite as a secondary binder phase for the densification and strengthening of 3D SiC manufactured using powder metallurgy technique.
We found that the silica nanowire growth rate and number density depend on the processing parameters such as NaOH concentration, sintering temperature, and time. Therefore, the goal of the first part of this dissertation is to investigate the effect of the processing parameters on nanowire growth and number density. Utilizing quantitative SEM image analysis and a silica nanowire growth model, the focus is on optimizing processing parameters to achieve maximum nanowire growth and density, ultimately enhancing the densification and mechanical properties of 3D printed SiC components. The silica nanowire was grown inside the pore of 3D printed SiC disc through the vapor solid (VS) noncatalytic mechanism. In this process silica (SiO2) vapor condensed directly onto the SiC particle surface, leading to the nucleation and growth of one-dimensional silica nanostructures. Differential scanning calorimetry (DSC) and thermogravimetric (TG) analysis were performed on SiC disc prepared via the powder metallurgy technique using NaOH solutions at varying concentrations (5%, 10%, and 20%). The thermal analysis helped us determine the nucleation temperature of silica droplets at 525 °C and crystallization temperature at 800 °C. The effect of NaOH concentrations analysis showed that the nanowire number density (mm-2) as well as the width and length of the nanowires increased according to the concentration of the NaOH used to pretreat 3D printed SiC in the order 20% > 10% > 5%. The optimal combination of NaOH concentration and heat treatment parameters identified for the highest nanowire number density and nanowire growth involved impregnating with 10% NaOH and heat treating at 550 °C for 6 hours and 1100 °C for 4 hours. The resulting sample exhibited a nanowire number density of 55431 ± 9232 mm-2, majority of the nanowires were in the width range of 0.3 µm – 0.6 µm, and length of 25.6 ± 3.3 µm as determined through quantitative SEM image analysis. The compressive strength, density and porosity were found to be 9.86 ± 1.4 MPa, 2.27 gcm-3, and 38.32%, respectively. Subsequently, a mathematical nanowire growth model was developed in order to investigate the growth mechanism and understand the effect of reaction kinetics on the nanowire growth. The model accounted for the reaction kinetics controlling the formation of silica molecule and its subsequent deposition on nanowire top surface contributing to the growth of the nanowire. The change in nanowire length relation with respect to different processing parameters obtained from the model showed a good agreement with the experimental data.
The silica gel layer on the surface activated SiC particles transforms into cristobalite (SiO2) upon heat treatment which serves as a binding agent that holds the SiC particles together. However, cristobalite has relatively poor mechanical strength and thermal properties compared to SiC. Therefore, in the second part of this dissertation, an in-situ mullite binding agent was formed which has superior thermomechanical properties compared to SiO2. Additionally, it has thermomechanical and chemical properties comparable to those of SiC. We have reported on using coal fly ash as a source of alumina (Al2O3) that reacts in situ with the silica (SiO2), oxidation product of SiC. The instantaneous mullite formation on the surface of SiC facilitated due to presence of minor concentrations of metal oxides in coal fly ash, resulted in a strong bonding zone between the two phases at relatively low temperature. In this work, SiC was mixed with coal fly ash at weight ratios of 90SiC/10ash, 85SiC/15ash, 80SiC/20ash, and 75SiC/25ash and sintered at 1400 °C. Measurements of mechanical properties showed that the 85SiC/15ash composition had the highest mechanical strength among samples. XRD analysis showed the phase composition of thermally treated 85SiC/15ash to be 81.8 wt% SiC, 11.4 wt% mullite, and 6.8 wt% cristobalite. SEM-EDX revealed a concentration gradient of Al in the cristobalite which enhanced formation of functionally graded bonding zones between phases and resulted in SiC-mullite composite with high thermomechanical properties. The compressive strength, nanoindentation elastic modulus, and Vickers hardness were 434 ± 20 MPa, 370.9 ± 22.6 GPa, and 11.5 ± 1.2 GPa respectively. The thermal shock resistance test showed high dimensional and mechanical stabilities after quenching in liquid nitrogen (−196 °C) from 1400 °C. The SiC-mullite composite showed low thermal expansion co-efficient from 3.17 x 10-7 /K to 5.615 x 10-6 /K when the sample was heated from 182 K to 354 K. The specific heat capacity, thermal diffusivity, and thermal conductivity were 7.83 ± 0.0014 J/g.K, 1.04 ± 0.013 mm2/s, and 17 W/m.K at 100 °C, respectively. The SiC-mullite composite exhibited moderate electrical conductivity of 3.48 x 10-2 S/m at 1000 °C. The resulting SiC-mullite composite is suitable for high temperature applications such as diesel motor parts, gas turbines, industrial heat exchangers, fusion reactor parts, high-temperature energy exchanger systems, and hot gas filters due to its high mechanical strength and thermal shock-resistance. This work demonstrated the potential of utilizing an in-situ mullite bonding agent instead of silica layer in additive manufacturing of SiC in the powder bed binder jet process for achieving a dense SiC parts with high thermomechanical properties.